Pre-cooling is one of the most important steps in poultry processing. After slaughter, the internal temperature of chicken must be reduced to ≤4°C as quickly as possible, with some processors requiring temperatures as low as ≤2°C. Traditional methods using flake ice and chilled water consume significant amounts of energy. The adoption of a chilled water recirculation system offers a more efficient alternative, reducing electricity consumption by approximately 25% to 35% while addressing operational challenges and enhancing market competitiveness.
We design refrigeration solutions tailored to the unique needs of each project, selecting the ideal refrigerants and system configurations to ensure optimal performance. With growing demands for environmentally friendly, safe, and energy-efficient technologies, we have developed CO₂-based refrigeration systems that provide exceptional reliability and efficiency. These systems are particularly suited for low-temperature applications, including individual quick freezers (IQF), quick-freezing chambers, and cold storage facilities, making them a preferred choice for medium- and large-scale poultry and seafood processing operations.
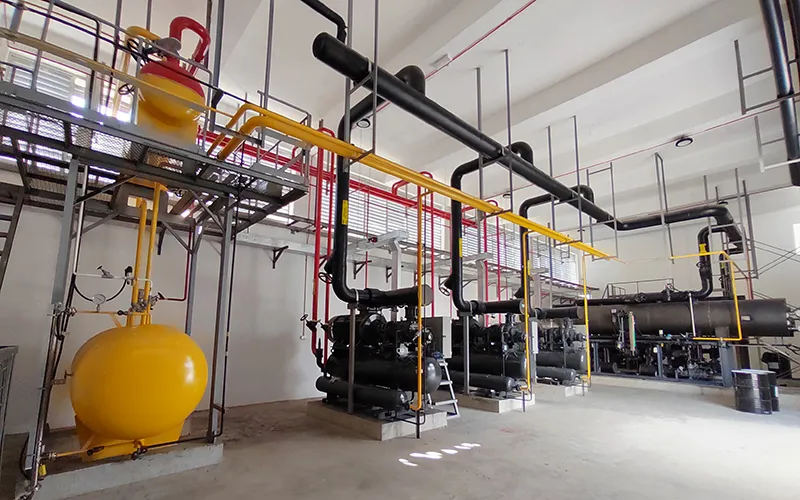
Recovering heat from refrigeration systems can significantly enhance energy efficiency in industrial operations. our innovative solutions utilize this heat through high-temperature heat pump units to produce hot water and steam, all without impacting the core refrigeration process. By seamlessly combining refrigeration and heating technologies, these systems achieve simultaneous cooling and heating, optimizing energy usage and maintaining a high coefficient of performance (COP). This design reduces dependency on boilers and electric heating equipment, offering a practical and cost-effective alternative.